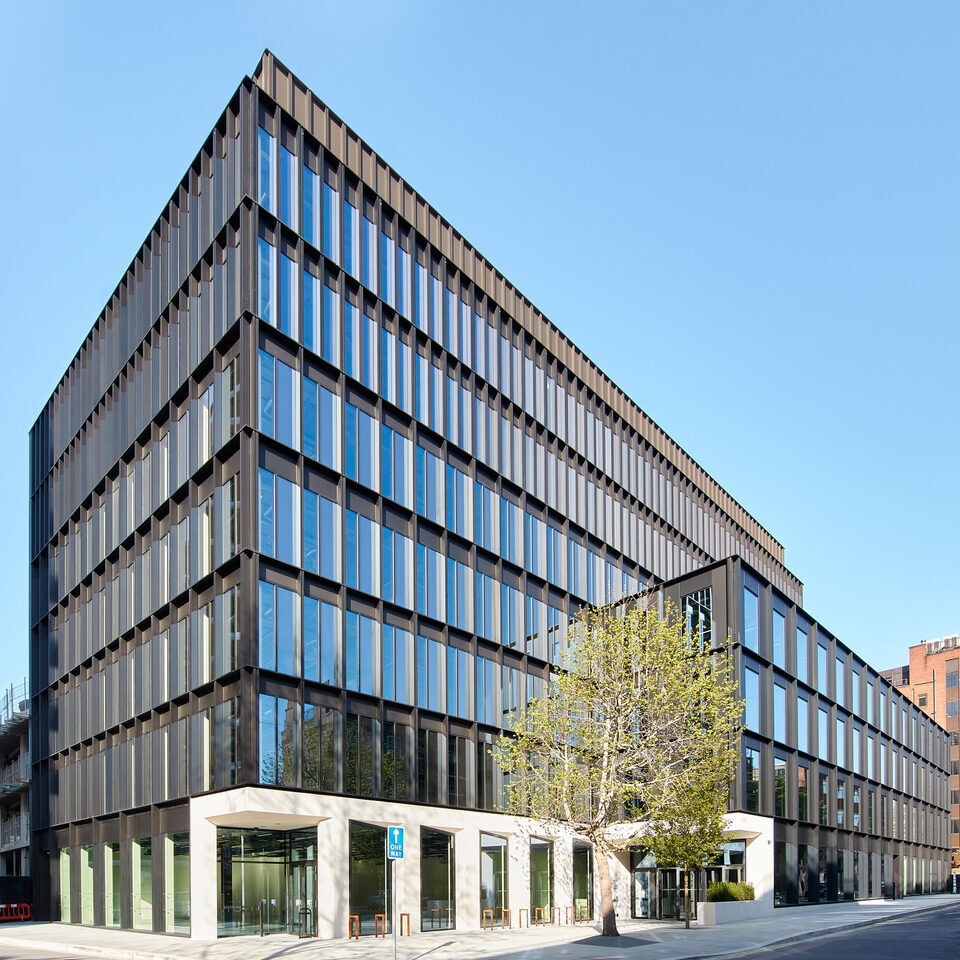
Letter from London
Leading the way on carbon-neutral offices
The drive to reduce, and where possible eliminate, carbon emissions continue to grip the property and construction sectors in the UK, writes Paul Finch.
While the new buzz word about offices and the areas in which they sit is ‘vibrancy’, it is difficult to legislate for that.
For policy-makers, it is much easier to focus regulation on factors which have numbers attached – and the focus continues to become tougher. How is the sector responding to the challenge of avoiding near-pariah status in the world of some environmentalist, who seem opposed to almost any form of new commercial construction?
If you want to see what leading from the front is all about, heading down to the Bankside area on the south side of the Thames and view The Forge, a development by property giant Landsec, which is its first ‘zero carbon’ office project. It is not just the company which is saying this; the design is in accordance with the UK Green Building Council net zero carbon framework, whose criteria have been met (with final performance subject to scrutiny of energy bills after a year of occupation). It is net zero carbon in terms of both construction and operation, is BREAM Excellent and WELL Gold.
There are two buildings totalling 139,000sq ft, the larger of which is 90,000sq ft, the smaller one run by Myo, Landsec’s flexible and fully-serviced office operation, connected by a courtyard. They replaced a humdrum warehouse and office on the site – the name Forge referring to previous industrial use as a bronze foundry on the site. Architects are Piercy & Co, with multi-disciplinary engineers and designers Bryden Wood playing a significant part in the thinking behind the building.
But the key team member behind the nine-storey project is Landsec’s head of design innovation, Neil Pennell, who has been ploughing the energy and productivity furrow for many years. His enthusiasm for the Forge project is huge, not least because it is the thinking behind what has been achieved that suggests that it can be a precedent project. ‘Design for Manufacture and Assembly’ principles were adopted, and combined with Modern Methods of Construction to analyse every aspect of how architecture, engineering construction and delivery could become exemplars of a synthetic approach which incorporated time-saving as a critical element of thinking.
Construction itself was undertaken by a first-time collaboration between contracting giants McAlpine and Mace, preceded by mock-ups of certain building processes on a redundant dairy farm in the West Country prior to introduction on site. The project was delivered via a construction management form of contract; everything came under scrutiny as the potential of the project to hit net zero generated innovative approaches; the basement was revamped and slashed in area to hit 2030 carbon targets (message: avoid basements if possible); boilers were eliminated and air-source heat pumps introduced; beams were bolted rather than welded, and a re-usable set of temporary works was used to created the floor slabs.
This involves a hybrid steel and concrete structural platform, which provided the chassis for the office floor space, while development of cladding and building services components created a reusable kit-of-parts.
Pennell points to the 18% of steel and 13% of concrete taken out of the initial estimates of what would be required. This resulted in around 40% embodied carbon reduction compared with a first conventional design; of this 50% came from changes to structure.
Aren’t experimental projects like this bound to be expensive? Pennell’s attitude to this is based on looking at the whole process of what is involved in creating a building. Where do prelims fit into the cost analysis? How do you reflect in the construction cost the time it takes to build? In the end, if you build it better and faster, making the most of prefabrication (tighter tolerances, factory accuracy), and factor in continuous improvement through re-use of the approach, it will work for you.
Founder Partner
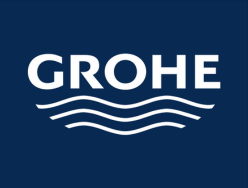